Teknoloji & İnovasyon
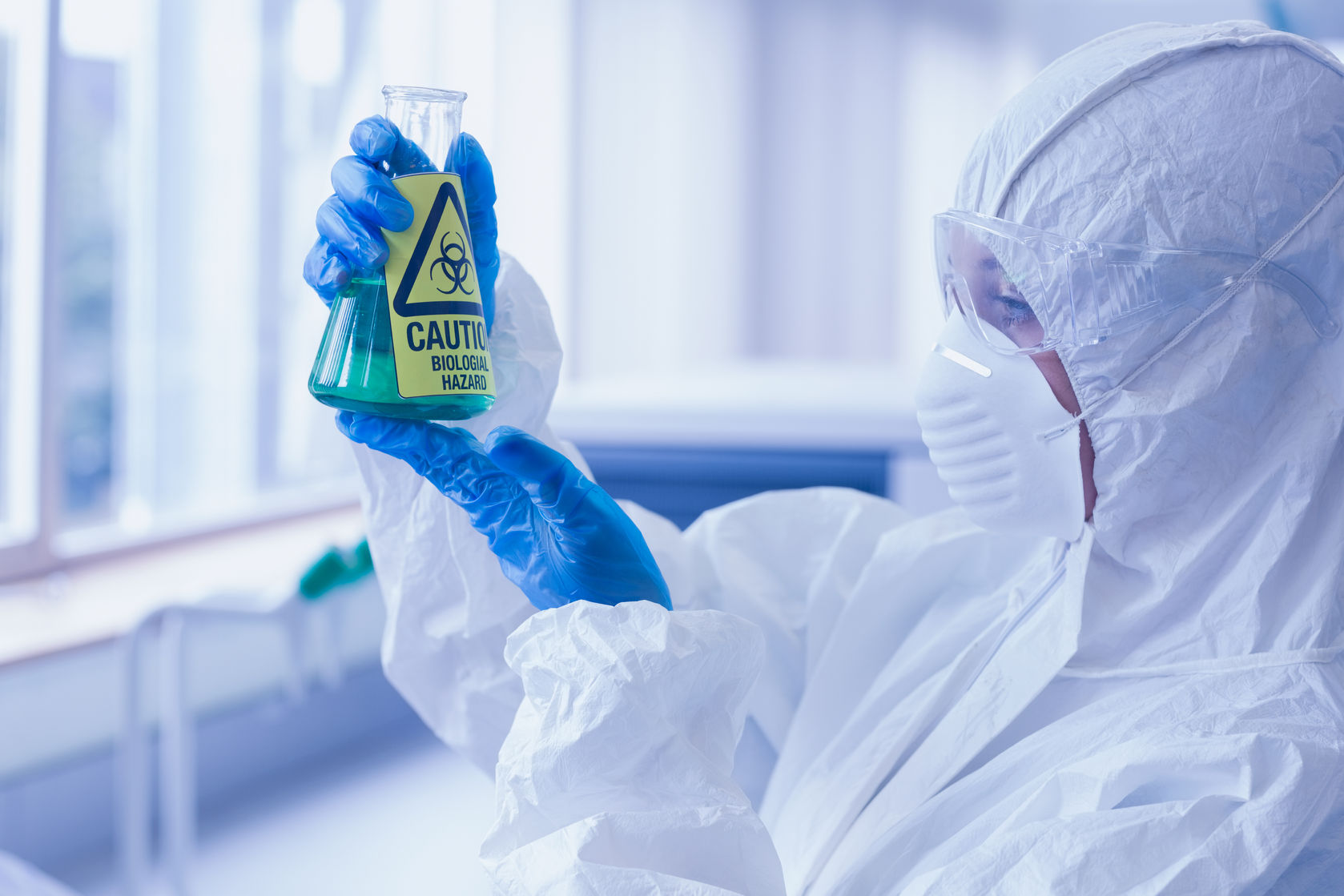
Temizoda Ekipmanlarının Partikül Kontrolünü Sağlayacak Şekilde Tasarlanması
31 Mayıs 2017, Ça
"Yeni ISO 14644 standardı ekipmanın uygunluğunu değerlendirmek için bir başlangıç noktası sağlar ve standartlara ek olanlar da dahil olmak üzere bu makalede ortaya konan hususlar, temizoda ekipmanının uygunluğunu değerlendirmek için bir kontrol listesinin temelini oluşturmada kullanılabilir."
Dr. Tim Sandle
Giriş
Temizodalar, HEPA ve ULPA filtreler sayesinde havadaki parçacıkların nüfuzunu en aza indirmek ve temizoda içinde üretilen partiküllerin kontrolünü sağlamak üzere tasarlanmıştır. Türbülans akışı gibi iyi bir hava tasarımı, partiküllerin yüzeylere çökelmesini önlemeye yardımcı olur (partiküller iki ana mekanizma ile çöker: yerçekimsel sedimantasyon ve türbülans çökelme) [1]. Oda havasının alınması/çekilmesi ve odaya temiz hava ilavesi (hava değişim oranları) yoluyla elde edilen partiküllerin giderilmesi ve havadaki partiküllerin daha az temiz bir havadan temizlik seviyesi daha iyi bir alana akışının engellenmesi pozitif basınç farkları ile sağlanır.
Temizodaların bu tasarım ilkeleri (hava akımı görselleştirme çalışmaları ile gözlemlenebilir) on yıllardır anlaşılmış ve benimsenmiş, kontrolün iyileştirilmesi için geliştirilen teknolojilerdeki ilerlemelerle güçlendirilmiştir [2]. Daha az üzerinde durulmuş olan şey ise temizoda içine giren ekipmanların özellikleridir.
Partikül oluşumu
Temizodalarda partikül oluşumunun ana kaynağı insanlardır. En uygun şekilde hazırlanmış temizoda giysileri dahi cilt hücrelerinin dökülmesiyle veya giysinin kendi elyaflı materyalinden ortaya çıkan partikülleri tutamaz [3]. Cilt parçacıkları yığınıyla taşınan bakteri veya mantar hava akımında belli sayıda mikrop taşıyıcı partikül birikimine sebep olacaktır. Parçacıkların ikincil bir kaynağı ise, yakın zamana kadar hakkında hiçbir standart bulunmayan, temizodalara yerleştirilen ekipmanlardır. Temizodalarda kullanılan pek çok ekipman olmasına ve bazı imalatçıların, ekipmanın belirli bir ISO sınıfında kullanılmasının uygun olduğu yönündeki iddialarına rağmen, bu ekipmanlar uygun bir tasarıma sahip değildir.
ISO 14644 Bölüm 14
Temizoda standartlarının ISO 14644 serisi 1999'da temizoda sınıflandırmasına yönelik Bölüm 1'in yayınlanmasıyla başladı [4]. Bunu 2001 yılında, uygunluğun sürekliliğini göstermek için gerekli adımları içeren Bölüm 2 izledi (1. ve 2. bölümlerin her ikisi de 2015 yılında güncellendi). O zamandan bu yana ISO 14644, yüzeylerin kimyasal kontaminasyonundan, yalıtıcılar gibi engelleyici araçların çalışmasına kadar olan alanları kapsayan bir dizi dokümana dönüştü. 2016'da, standardın yeni bir bölümü çıkarıldı: ISO 14644: 14 (2016) "Havadaki partikül konsantrasyonu ile ekipman kullanımı için uygunluğun değerlendirilmesi." [5]
ISO 14644-14: 2016, havadaki partikül temizliğine ekipmanların etkisi bakımından temizoda ve ilişkili kontrollü ortamlarda kullanılmak üzere ekipmanın (örneğin, makine, ölçüm cihazı, proses ekipmanı, parça ve aletler gibi) uygunluğunu değerlendirmek için kullanılabilecek metodolojiyi belirtir. Standart, temizoda ekipmanlarının ISO 14644-1'de belirtilen partikül kontrol şartlarını karşılamasını sağlayacak şekilde geliştirilmiştir. Gerekli kontrol seviyesi temizoda sınıfına bağlı olacaktır; burada ISO 14644: 14, 0.1 μm'den 5.0 μm'ye eşit veya daha büyük boyutlara kadar değişen partikül boyutları kapsar. Standardın odağı, ayrışmamış partiküllerdir ki bu da biyolojik kontaminasyona özel olarak değinilmediği anlamına gelir. Bu, biyolojik kontaminasyonun önemli olmadığı anlamına gelmez, çünkü yüzeyler üzerindeki mikroorganizmaların bir kısmı (bir aktarım katsayısı olarak ifade edilir), nesneler veya personel teması ile yüzeylere veya yüzeylerden aktarılır [6]. Standart ayrıca ekipmanın tasarımına da odaklanır ve temizlenebilirlik açısından gelecekteki kullanımlarına değinmez.
Temizodalar için ekipmanların tasarlanması
ISO 14644: 14 kılavuzuna dayanarak, temizodalar için ekipmanlar nasıl tasarlanmalıdır ve temizoda yöneticileri bu konuda nelere dikkat etmelidir? Makalenin bu bölümünde dikkat edilmesi gereken bazı önemli noktalar açıklanmaktadır:
Malzemelerin seçimi: Ekipman için tercih edilen malzeme düz/pürüzsüz, temizlenebilir olmalı ve düşük partikül emisyonuna sahip olmalıdır. Pasif partikül oluşumunu engellemek için kaplama veya oksit kaplı çelik yerine paslanmaz çelik tercih edilmelidir. Boya kullanılmamalıdır.
Gerekli olduğu durumlarda ekipmanın üzerine yapışabilecek partiküllerden korunabilmesi için düşük elektrostatik özelliklere sahip olması gerekir (bu, mikroorganizmalar da dahil olmak üzere partiküllerin hava yoluyla taşınmak yerine ekipmanın yüzeyine bağlandığı elektrostatik çekim fenomeniyle ortaya çıkar). Havadaki partiküllere göre farklı bir yüke sahip ekipman, partiküllerin bağlanmasına yol açar ve yerçekimi, aerodinamik veya yapışma kuvvetleri için ayrı bir risk faktörü sunar.
En çok etkilenen malzeme türleri cam, teflon ve polimerler gibi yalıtım malzemeleridir. Bu malzemeler yüksek oranda çekim yükü içerir. Plastik ya da diğer yalıtıcı cihazlarla temasa girdiğinde bu sorun daha da şiddetlenir ve bu durumda daha fazla statik yük üretirler.
Yüzey direncinin yükselmesi ve bağıl neme maruz kalması nedeniyle göz önüne alınması gereken bir değişken de temizoda ortamıdır. Bu nedenle, ekipman yüzeylerinin statik yükünü kontrol etmek için temizoda sıcaklık ve nem kontrolünün yapılması gereklidir.
Malzeme seçimi ile ilgili diğer bir nokta ise, temizoda sıcaklık değişimlerine ve ekipmanın operasyonel sıcaklığına bağlıdır; malzemeler iyi termal özelliklere sahip olmalı ve sıcaklık artışı ile fiziksel değişimlere maruz kalmamalıdır.
Reaktif olmayan yüzeyler: Bileşenlerle, proses materyalleri veya ilaç ürünleriyle temas eden biyofarmasötik yüzeyler, reaktif, katkılı veya soğurgan/emici olmamalıdır.
Ekipmanın tasarımı: Ekipman tasarımı, mümkün olduğu kadar kolay temizliğe izin vermeli ve emici yüzeyleri en aza indirmelidir. Tasarım ayrıca, düz/pürüzsüz ve çatlaksız olması gereken yüzeyler sayesinde partikül oluşumunu da minimize etmelidir. Bu hususlar, “Kalite Tasarımı” felsefesiyle yakından ilişkilidir.
Partiküller, pasif (yukarıda anlatıldığı gibi) veya aktif olarak üretilir. Aktif partikül üreticileri arasında konumlandırma aşamaları ve lineer rulman blokları, yuvarlak civatalar ve diğer metalik bant contaları gibi kaygan yüzeylere sahip diğer bileşenler bulunur.
Ekipman işlevselliğinin bu yönleri, partikül oluşumunun en aza indirgeneceği şekilde tasarlanmalıdır. Cihaz gövdesinin üzerine sürülen ve partikül üretebilen harici elektrik kablolarına ve hava hortumlarına da ayrıca dikkat edilmesi gerekir.
Sızdırmazlık malzemeleri/contalar partikül oluşumunun bir kaynağı olabilir, ki bu da karbon siyahının uygun olmadığı, buna karşın daha az partikül üretimine sebep olacakları için aşınmaya dirençli boş üretanların daha uygun oldukları anlamına gelir.
Contaların kendileri, metaller veya kayışlardan yapılmış contalar ile kayış sızdırmazlık sistemleri genellikle metal sızdırmazlık sistemlerine göre daha düşük sürtünmeye sahiptir ve tercih edilirler. Buna ek olarak, rulmanlar ve bilyalı vidalar da izole edilmelidir.
Yağlayıcı maddeler: Yağ buharı ve damlacıkları, rulman ve aktarma cihazlarında kullanılan yağlayıcılardan havaya dağıtılabilir. Bu nedenle temizoda sınıfı yağlayıcıların belirlenmesi gerekir (vakum derecesi, düşük buhar basıncı gibi). Çoğunlukla gıda sınıfı yağlayıcılar uygun olmasına rağmen partikül boyutu ve oluşumu da değerlendirmeye alınmalıdır.
Temizlenebilirlik: Ekipmanlar için kolay yüzey temizliği henüz standartlarla belirlenmemiş olmasına rağmen yüzeylerin ne kadar kolay temizlenebildiği önemli bir değerlendirme aracıdır. Ekipmanlar, temizlik, bakım ve diğer ilgili işlemleri kolaylaştırmak adına uygun bir boyut, yapı ve konumda olmalıdır.
Burada göz önünde bulundurulması gereken faktörler, aşınmaya neden olan maddeler gibi ekipmana zarar vermeyecek en uygun temizleme reaktiflerini seçmek veya silme işlemi vasıtasıyla aşırı partikül oluşumuna neden olmaktır. Bir yüzeydeki aşınma ve çatlaklar, mikroorganizmaları barındırabilecekleri ve dezenfektanlar sabit organizmaları etkisizleştirmek için buralara nüfuz edemeyebilecekleri için önemlidir [7].
Özet
İyi bir temizoda tasarımı önemlidir. Buna ek olarak, temizodalara giren ekipmanın tasarımı da özen gerektirir. Bu gereksinim, bazı imalatçılar tarafından temizoda ekipmanının uygunluğuna göre değerlendirilirken, bu değerlendirmede ya bazı ürünler uygun bulunmaz ya da düzgün bir şekilde değerlendirilmez. Yeni ISO 14644 standardı ekipmanın uygunluğunu değerlendirmek için bir başlangıç noktası sağlar ve standartlara ek olanlar da dahil olmak üzere bu makalede ortaya konan hususlar, temizoda ekipmanının uygunluğunu değerlendirmek için bir kontrol listesinin temelini oluşturmada kullanılabilir.
Referanslar
[1] Whyte, W., Agricola, K, ve Derks, M. (2015) Airborne particle deposition in cleanrooms: Deposition mechanisms, Clean Air and Containment Review, 24, s.4-9
[2] Sandle, T. (2012). Airflow visualisation in an aseptic facility, Cleanroom Technology, 20 (5): 13-17
[3] Reinmüller, B. (2001). People as a Contamination Source - Clothing Systems. In Dispersion and Risk Assessment of Airborne Contaminants in Pharmaceutical Cleanrooms. Royal Institute of Technology, Building Services Engineering Bulletin, No. 56, Stockholm, s.54-77
[4] Sandle, T. ve Saghee, M.R. (2017). Cleanroom certification and ongoing compliance. In: Sandle, T. ve Saghee, M.R. Cleanroom Management in Pharmaceuticals and Healthcare, Euromed Communications: Passfield, UK, s.169-184
[5] ISO 14644-14:2016 Cleanrooms and associated controlled environments. Assessment of suitability for use of equipment by airborne particle concentration, International Standards Organizartion, Geneva
[6] Whyte, W., ve Eaton, T. (2015) Microbial transfer by surface contact in cleanrooms. European Journal of Parenteral and Pharmaceutical Sciences, 20(4), s.127-131.
[7] Sandle, T. (2016). Cleaning and Disinfection. In Sandle, T. (Ed.). The CDC Handbook: A Guide to Cleaning and Disinfecting Cleanrooms, Grosvenor House Publishing: Surrey, UK, s.1-31
__________________________________________________________
Yazar Hakkında
Dr. Tim Sandle mikrobiyolojik araştırma ve biyofarmasötik süreçlerdeki 25 yılı aşkın tecrübesiyle alanında uzman bir biyologdur. Keele Üniversitesi’nden doktora derecesine sahip Sandle, farmasötik mikrobiyoloji ve temizoda kontaminasyon kontrolü konularında pek çok ulusal ve uluslararası komitede görev yapmaktadır. Sandle ayrıca ilgili alanlarda sayısız yayına da imza atmıştır.
__________________________________________________________
Orijinal Metin
Good design of cleanroom equipment to meet particle control
Introduction
Cleanrooms are designed to minimize the ingress of airborne particles (which is achieved through HEPA or ULPA filters) and to control what happens to particles generated within he cleanroom. With particle counts good air design, such as turbulent flow helps to prevent particles from being deposited onto surfaces (particles settle by two primary mechanisms: gravitational sedimentation and turbulent deposition) (1). The removal of particles in achieved through extraction of room air and the addition of clean air into the room (air exchange rates) and the blocking of the flow of particles in air from a less clean air to an area of a higher cleanliness level through positive pressure differentials.
These design principles of cleanrooms (observable through airflow visualization studies) have been understood and have been in place for decades, enhanced through advances in technology aimed at improving control (2). What is less well-defined are specifications for the equipment going into cleanrooms.
Particle generation
The main source of particle generation in cleanrooms is people. Even the best prepared cleanroom garments will not contain all particles produced by the shedding of skin cells or from fibrous material from the garment itself (3). A given number of particles deposited into the air-stream will be microbial carrying particles where bacteria or fungi are carried on rafts of skin detritus. A secondary source of particles and one, until recently, where no standard has existed is from the equipment placed into cleanrooms. All too often the equipment placed in cleanrooms is not of a suitable design. This has been despite claims from some manufacturers that the equipment is suitable for use in an area of a given ISO class.
ISO 14644 Part 14
The ISO 14644 series of standards for cleanrooms began in 1999 with issuing of part 1 of the standard aimed at cleanroom classification (4). This was followed by part 2 in 2001, which covered the steps required to demonstrate continued compliance (both parts 1 and 2 were updated in 2015). Since then ISO 14644 has expanded into a series of documents covering areas from the chemical contamination of surfaces to the operation of barrier devices like isolators. In 2016 a new part of the standard was issued: ISO 14644: 14 (2016) “Assessment of suitability for use of equipment by airborne particle concentration.” (5)
ISO 14644-14:2016 specifies the methodology that can be used to assess the suitability of equipment (such as machinery, measuring equipment, process equipment, components and tools) for use in cleanrooms and associated controlled environments in terms of the contribution of the equipment to airborne particle cleanliness. The standard was produced so that equipment situated in cleanrooms meets the requirements of particle control stipulated in as specified in ISO 14644‑1. The level of control required will depend on the class of the cleanroom; here ISO 14644: 14 extends to particle sizes range from 0.1 µm to equal to or larger than 5.0 µm. The focus of the standard is with undifferentiated particles, which means that biocontamination is not specifically addressed. This does not mean biocontamination is not important since a portion of microorganisms on surfaces (expressed as a transfer coefficient) are transferred to and from surfaces by connecting objects or personnel touch) (6). The standard also focuses on the design of the equipment and it does not address its future use in terms of cleanability.
Design of equipment for cleanrooms
Based on the ISO 14644: 14 guidance, how might equipment be designed for cleanrooms and what should cleanroom managers be looking for? This section of the article discusses some important points to note:
• Selection of materials: The types of materials selected for equipment need to be smooth, cleanable and to have low particle emissions. To avoid passive particle generation stainless steel in recommended in place of plated or oxide-coated steel (which can shed particles). Paints must always be avoided.
Where required the material should have low electrostatic properties to avoid particles adhering to the equipment (this arises through the phenomenon of electrostatic attraction where particles, including microorganisms, are bound onto the surface of equipment instead of remaining airborne). Equipment with a different charge to airborne particles leads to the potential for particles binding and it presents a separate risk factor to gravitational, aerodynamic, or adhesion forces.
The types of material most affected include insulating materials such as glass, Teflon, and polymers. These items can become highly charged. The problem is exacerbated when plastics or other insulative devices are contacted, rubbed, or handled; here they generate higher static charges.
A related variable that needs to be considered is the cleanroom environment, since surface resistance rises and falls with relative humidity and therefore control of the cleanroom temperature and humidity is often necessary for controlling the static charge of equipment surfaces.
A further point in relation to material selection is that depending upon the temperature ranges of the cleanroom and the operational temperature of the equipment; the materials should have good thermal properties and not be subject to physical changes with an increase in temperature.
• Non-reactive surfaces: For biopharmaceuticals surfaces that contact components, in-process materials, or drug products must be non-reactive, and not be additive or absorptive.
• Design of equipment: The equipment design should promote cleanability and minimize occluded surfaces where possible. The design should also minimize particle generation in that surfaces should be smooth, contain as few joints and cracks. These considerations are pertinent to the philosophy of Quality by Design.
Particles are generated passively (as discussed above) or actively. Active generators of particles include positioning stages and other components with sliding surfaces like seals on linear-bearing blocks, ball screws, and other metallic strip seals. These aspects of the equipment functionality need to be designed so that particle generation is minimized. Attention also needs to be paid to external electrical cables and air hoses, which can rub over device housings and produce particles.
Sealants can be a source of particle generation which means that carbon black is unsuitable whereas unfilled urethanes that can resist abrasion will be more suitable in that they generate fewer particles. With seals themselves, seals made from metals or belts, belt-sealing systems generally have substantially lower friction than metal-sealing systems and are preferred. In addition, bearings and ball screws should be isolated.
• Oils and lubricants: Oil vapors and droplets can be dispersed in the air from lubricating oils used in bearing and drivetrain devices. For this reason cleanroom grade lubricants need to be selected (such as vacuum-grade, low-vapor pressure, low-migration grease). Often food-grade lubricants are suitable, although the particle size and generation needs to be evaluated.
• Cleanability: Although the ease of cleaning the surfaces of the equipment is not immediately addressed by the standard, how easy the surface is to clean is an important consideration. Equipment should be of a suitable size, construction, and location to facilitate cleaning, maintenance, and proper operations.
Factors to consider here are with selecting the most suitable cleaning reagents, such as ones that will not damage the equipment (such as causing abrasions) or lead to the excessive generation of particles through the act of wiping (a consideration for the quality of wipers as well as the interaction between equipment and the wipe and cleaning chemical). The presence of abrasions and cracks to a surface are important since these can harbor microorganisms and disinfectants may be unable to penetrate to inactivate the sessile state organisms (7).
Summary
Good cleanroom design is important. In addition the design of the equipment going into cleanrooms also requires attention. While this requirement has been considered by some manufacturers in relation to the suitability of equipment going into cleanrooms, some products are unsuitable or they have not been properly evaluated. The new ISO 14644 standard provides a starting point for assessing equipment suitability and points raised in this article, including those additional to the standard, can be used to form the basis of a checklist to assess the suitability of cleanroom equipment.