Teknoloji & İnovasyon
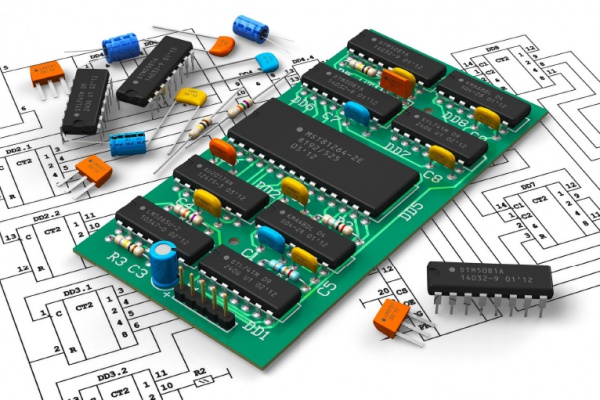
TÜMDEVRE TEKNOLOJİLERİ
26 Kasım 2018, Pt
Atakan Peker – YİTAL Mikroelektronik AŞ Volkan Özgüz – Sabancı Üniversitesi
Tümdevreler hayatımızın her evresinde bize görünmez bir şekilde destek olan elektronik yapıtaşlarıdır. Bilgisayarlarımız, cep telefonlarımız, otomobillerimiz, enerji sistemleri, fabrikalarımız tümdevreler tarafından kontrol edilirler. Tümdevereler elektronik baskılı devreler üzerinde koyu renkli plastik veya seramik kılıflar içinde bulunurlar. Tümdevreler transiztörler, dirençler ve kapasitörler gibi elektronik devre elemanlarının mikron altı veya nanometre boyutlarda silisyum bir taban üzerinde birleştirilmesinden oluşurlar. Günümüzde tipik bir tümdevrede milyonlarca devre elemanı bulunur.
Nanometrik boyutlarda transzistörleri gösteren tipik bir modern tümdevre kesiti
Yarıiletken teknolojilerinde ve özellikle tümdevrelerin karmaşıklığında baş döndürücü bir hızla gelişmeler olmaktadır. Intel firmasının kurucularından Gordon Moore’a atfedilen bir uzun soluklu tahmin yaklaşımına göre, tümdevrelerde transistor yoğunluğu başta olmak üzere birçok performans parametresi 18-24 ayda iki misline katlanmaktadır (Moore Kanunu). Eğer otomotiv teknolojileri aynı hızla gelişseydi bir otomobilin yakıt tüketimi on yıl öncesinin %1-2 si civarında olması gerekirdi.
Tümdevre yapılarının üretimi “yarıiletken” dediğimiz malzeme teknolojileri ile mümkün olmaktadır. Yarıiletken üretim teknolojileri mikroskobik yapıları (metrenin milyarda bir ölçeğinde) ve çok aşamalı süreçleri nedeniyle diğer malzeme ve donanım teknolojilerinden ve diğer tipik yüksek teknoloji üretim tesisinden (örnek otomotiv, elektronik cihaz üretimi vb.) temel farklılıklar göstermektedir. Örnek olarak üretim tozsuz alanlar olan temizodalarda yüksek saflıkta kimyasallar kullanılarak yapılmaktadır.
Günümüzde yarıiletken üretim teknolojileri farklı ihtiyaçlara bağlı olarak çeşitlenmiş olmakla birlikte CMOS teknolojileri temel teknoloji olma özelliğini korumaktadır.
Complementary Metal Oxide Semiconductor (Bütünleyici Metal Oksit Yarı İletken) kelimelerinin baş harfleri ile kısaltılan CMOS, çok çeşitli uygulamalar için kullanılabilen esnek ve nispeten düşük maliyetli bir üretim teknolojisidir. Birim silisyum alanda en fazla transistör sayısına sahip olması, düşük gürültülü olması ve statik (açık durumda fakat işlem yapmıyorken) güç tüketiminin neredeyse hiç olmaması sebebiyle başta tümdevre tasarımı olmak üzere birçok alanda oldukça yaygın olarak tercih edilmektedir.
Teknoloji gelişiminde referans olması ve karşılaştırma imkânı sağlaması açısından boyutlar rastgele değil belli aralıklarla küçültülür. Örneğin; 250 nm, 180 nm, 130 nm, 65 nm vb. boyutlardaki küçülmenin arkasındaki itici güç belli bir kırmık alanına olabildiğince fazla transistor sığdırmanın yarattığı maliyet indiriminden kaynaklanır. Ancak bu işlemin bedeli artan cihaz maliyetleri ve üretimde kullanılan pul (wafer) denilen ve çapları 100-450 mm civarında olan silisyum tabanların üretilmesindeki artan maliyet olarak ödenir. Bu açıdan mikroelektronik teknoloji adımı (node) seçimi bir optimizasyon gerektirir. Artan cihaz maliyetleri ve görece pul maliyeti, bir pul üzerinde bulundan kırmık sayısının artması ile dengelenebilir ve hatta kırmık başına maliyet daha azalabilir. Orta teknoloji adımlarında maliyet hassasiyeti daha optimum bir seviyede bulunabilir.
Boyutlarda küçülmenin bir başka faydası güç tüketiminin azalmasıdır. Günümüzde bir işlemci, geçmiş zamanlarda kW’larca güç harcayarak yapılan bir bilgi işlem dizinini 10-20 W güç harcayarak yapabilmektedir.
Yarıiletken ve mikroelektronik sektörünün en temel farklılıklarından biri diğer sektörlere göre çok daha hızlı yenilenmesi gereken özel üretim tesisleri, özel ve karmaşık cihazlara ihtiyaç duymasıdır. Bu farklılık nedeniyle yarıiletken üretim teknolojilerinin oluşturulması ve kurulması çok zahmetlidir.
Tümdevre (IC) gerçekleştirilmesinde ilk adım tasarımdır. Daha sonra tasarımın yarıiletken üretim teknolojileri kullanılarak üretilmesi (Fabrication) aşaması gelir. Bu üretim pul (wafer) adı verilen birkaç yüz milimetre çapındaki Silisyum diskleri üzerine yapılır. Bir pul üzerinde yüzlerce hatta binlerce kırmık bulunabilir. Bu aşamadan sonra pul bir ön test işleminden geçirilir. Daha sonra özel cihazlarla kesilerek her bir kırmık paketlerin (kılıfların) içine yerleştirilir. Yerleştirilen bu kırmıkların giriş ve çıkış noktaları paketin giriş ve çıkışlarına çok ince tel (wire bonding) veya çok küçük lehim noktaları (bump bonding) ile bağlanır ve kırmığın çalışması test edilir. Bu son işlem adımları ise Assembly/Test olarak adlandırılır. Üretimi tamamlanan kırmıklar farklı ürünlerde yer almak üzere sistem firmalarına aktarılmaktadır.
- Öncelikle tasarıma konu olacak kırmığın sahip olması gereken özellikler belirlenir.
- Sayısal ve analog simülasyonları gerçekleştirilen tasarım, proses tasarım kiti (PDK) yardımıyla sürekli olarak simülasyonlar ile yenilenir ve düzenlenir.
- Bu düzenleme üretim evine gönderilmeden önce prosesi tasarlayabilmek adına üretim evinin sahip olduğu Proses Tasarım Kiti (PDK) yardımı ile işlem adımları belirlenir ve tasarım buna göre düzenlenerek ilgili tasarım layout – serim hâline getirilir.
- Layout hâline getirilmiş tasarım ve ilgili üretim adımları doğrulama adımından geçerek üretim evine iletilmek üzere özel bir formatta (.gds) dosyalar oluşturulur.
- Bu formatta dosyası oluşturulmuş tasarımın, üretilebilmesi için en önemli aşama olan maske yazımı yapılmak üzere maske yazım tarafına gönderilir.
- Litografi için hazırlanan maskeler ile üretim evindeki aşamalar başlamış olacaktır.
- Üretim evinde gerçekleşen üretimler sonrası pul test edilir ve dilimleme ve kılıflama işlemleri gerçekleştirilir.
Tümdevre üretimi mikrometre ve nanometre (milimetrenin binde ve milyonda biri) kalınlığında birden fazla ince metal ve yalıtkan katmanların arka arkaya oluşturularak fotolitografi adı verilen özel pozlama ve aşındırma yöntemleri ile nanometre boyutlarında şekillendirilmesi ile yapılır. Bu işlemler modern bir tümdevre için 300-400 ayrı adımda uygulanır.
1. aşama ile silisyum kütükten silisyum pullar çıkarılıp hazırlanmaktadır. Hazırlanan silisyum pullar, kontrol edilip ayrıştırılır ve oksitleme bölümüne geçer.
Alt taban hazırlığı adını verebileceğimiz 2. aşamada silisyum pullar oksitlenmektedir.
Buradan 3. aşamaya geçen pullar, litografi aşaması için ışığa duyarlı polimer malzeme ile kaplanmaktadır. Kaplama işlemi spin-coat adı verilen döndürerek kaplama ile yapılmaktadır. Bu aşamayı öncü ve takip eden ısıtma ve hazırlama evreleri izler ve takiben oksitlenmiş silisyum pullar litografi sistemi için hazırlanmış olur.
4. aşama litografi işlemidir. Kaplanan malzemenin ilgili maske ile şekillendirilmesi olarak da adlandırılabilecek bu aşamada, malzeme belirlenen dalga boyu ve uygulama aşamasına göre işleme tabi olup maskedeki desen pul üzerine aktarılır.
5. aşamada aktarılan desenin yüzeye inebilmesi için kimyasal aşındırma yapılır ve ışığa duyarlı aktifleşmiş malzeme aşındırılarak yüzeye indirilir.
6. aşamada izlenebileceği gibi oksit tabakasına desenin indirilmesi için hazırlanır. 6. aşamada oksit tabakası aşındırılarak ışığa duyarlı polimer malzeme temizlenir.
7. aşama ilgili desene istenilen özelliğin katılması için yapılır. Katıklama adını vereceğimiz bu işlemde silisyum yüzeyine iyon bombardımanı yapılarak desen yüzeyine istenen özellikler kazandırılır.
8. aşama ile hazırlan yüzey üzerine metal kaplama işlemi yapılır ve böylece ilk katman oluşturulmuş olur.
8. aşama sonrası, aynı işlemler 3. aşamadan itibaren teknoloji ve tasarıma göre 30, 40 defa tekrarlanır ve katmanlar hazırlanır.
9. aşamaya gelen silisyum pul kesilme işlemine hazırdır. Öncü testler sonunda kesilen pul, bağlama ve kılıflama adımlarını izleyen 10 ve 11. aşamanın ardından kullanıma hazırlanır.
İzlenen adımlar ve tekrarlar sonrası devre tamamlanıp son kılıflamaya hazır hâle getirilir.
Tümdevre üretiminde maske setlerinden yararlanılmaktadır. Her tümdevre üretimi için kullanılan teknolojiye uygun maskelerin önce üretilmesi gerekmektedir. Üretilen bu maskeler tümdevrenin üretim aşamalarında kullanılmaktadır. Bir maske setinin maliyeti teknoloji ilerledikçe artmaktadır. Yıllar geçip teknolojinin kullanımı arttıkça maske setlerinin maliyetleri de azalmaktadır. Örneğin 90nm teknolojisinin üretimde ilk kullanılmaya başladığı 2004 yılında bir maske seti yaklaşık 2 Milyon USD seviyesindeydi. Bugünlerde aynı teknolojide bir maske seti yaklaşık 200 bin USD seviyesindedir
Tümdevre teknolojilerin gelişimine bakıldığında üç ayrı eğilim görülmektedir. Litografi olarak yıllardır kullanılmakta olan ultraviyole (UV, i-line) pozlama, 130 nm civarında yerini derin ultraviyole (Deep UV) pozlamaya bırakmaktadır. Malzeme tarafında ise 65nm CMOS teknoloji adımında küçülen yatay ve dikey boyutlardan ötürü yeni bir malzeme grubu (örnek yüksek dielektrik katsayılı malzemeler) kullanılmaktadır.
Tümdevre teknolojilerinin güncel gelişimi
65nm ve 90nm CMOS teknolojileri genelde 200mm çaplı pullarla üretilmekte, 65nm’den küçük boyutlara sahip teknolojiler ise 300mm veya daha büyük pul çapı ile üretilmektedir. Pul çapı büyüdükçe cihaz maliyetleri artmaktadır.
Atomik boyutlara yaklaşan bu devrelerin üretimi için yarıiletken üretim evlerinde oldukça özgün, hassas ve karmaşık nitelikte cihazlar kullanılmaktadır. Üretim olağanüstü derecede tozsuz ortam (temizoda standartları) gerektirir. Üretim hattındaki duvarlar, tabanlar, su ve gaz borularına kadar varan birçok yapısal bileşende özel malzemeler kullanılmaktadır. Üretimde iyonik ve atomik seviyede saflık ve temizlik şartı (ppm to ppb) olduğundan çok yüksek saflıkta kimyasallar ve malzemeler kullanılması gerekmektedir. Bu tür ortamlarda çalışanların özel nitelikleri, eğitimi ve uygun bir zihniyeti olmalıdır.
Sektörde bilgi birikimine sahip insan gücü yetişmesi uzun zaman aldığı için yetişmiş insan gücünün değeri, cihazların aksine yıl geçtikçe daha da çok artmaktadır.
Tümdevre üretiminde kullanılan temizodalar temiz hava içinde bulunan parçacıkların boyut ve sayılarına göre sınıflandırılırlar. Son yıllarda kullanılan ISO 14644 standardında sayılar bir meterküp hava içinde 0,1 mikrondan daha büyük parçacık sayısının ondalıklı logaritmasın ifade eder. Örnek ISO 5 sınıfı bir temizodada 1 m3 havada 100.000 den daha az parçacık bulunur.
Çok temizodaların işletim maliyetleri çok yüksektir. Son yıllarda robotik otomasyonun artması ile tümdevre üretimi cihaz kapalı hacimleri içinde yapılarak büyük alanların temizlik sınıfları daha esnek seçilebilir. Silisyum pullar cihazlar arasında kapalı kutular içinde nakledilir. Cihaz üreticileri FOUP (Front Opening Universal Pod) adı verilen standartlaşmış arayüzler ve taşıyıcılar kullanırlar.