Dosya
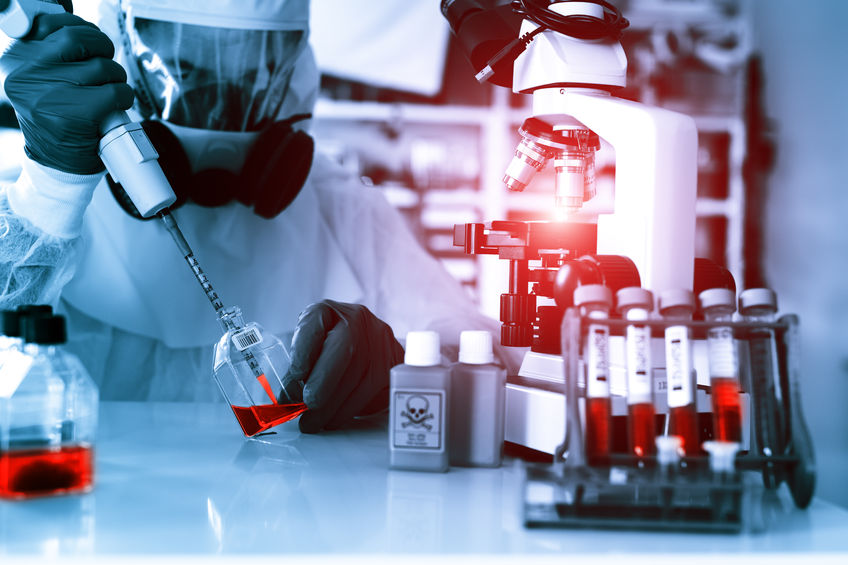
Temizoda Tarihçesi, Validasyonu ve İzlenmesi
29 Kasım 2017, Ça
E. Dilek Sunar
1. Özet
Tarihçesi çok uzun yıllara dayanan temizoda; sıcaklık, havadaki canlı-cansız partiküller, bağıl nem, basınç farkı ve hava akışı gibi çevresel faktörlerin kontrol altında tutulduğu modüler bir çevredir.
Temizoda validasyonu; tesisin, tasarım amacı ile tesis, ekipman ve çevrenin “Kullanıcı Gereksinimleri Spesifikasyonları (URS)” ile uyumlu olmasını sağlamak; bu faktörlerin tanımlanmış yasal gereklilikleri karşıladığından emin olmak ve tanımlanan standartları karşılayan bir sistem olarak birlikte işlev görmesini sağlamak gibi çeşitli nedenlerle gerçekleştirilmektedir.
Temizodalar yukarıda belirtilen kriterleri karşılamak amacıyla valide edilir ve sonrasında seçilen bir ISO 14644-1 sınıfına göre sertifikalandırılır.
2. Giriş
Temizoda Tarihçesi
Temizoda dizayn prensipleri yaklaşık 150 yıl öncesinde hastanelerde bakteri kontrolünü sağlamak amacıyla başlamıştır. 1939–1945 yıllarında modern temizodaların geliştirilmesi ise, İkinci Dünya Savaşında silah endüstrisinde kullanılan cihazların kalitesini ve güvenilirliğini artırmak için gerçekleştirilmiştir.
Bu süre zarfında en önemli gelişme HEPA filtrelerde yaşanmıştır. Üretim ve askeri amaçlı temizodalar geliştirilirken, hastanelerde de kontaminasyon kontrolü için havalandırmanın önemi artıyordu. 1950'li ve 1960'lı yıllarda NASA'nın uzay yolculuğu programının bir sonucu olarak temizodaların evrimi hız kazandı.
Bu süreçte temizoda teknolojisinde bir dönüm noktası olan "laminer akış" kavramı tanıtıldı. Sandia Ulusal Laboratuarları, temizodalarda bulunan aşırı kontaminasyon düzeylerini araştırmaya başladı. 1960'da Birleşik Krallık Middlesbrough'daki Blowers and Crew, bir ameliyathanede tüm tavana monte edilmiş hava difüzöründen tek yönlü hava akışı yaratarak kontaminasyon kontrolünü geliştiren ilk kişiler oldu. Uygulamalarda, hava akımının diğer hava akımları ve insanların hareketi tarafından bozulduğu görülünce tek yönlü akış fikri doğmuş oldu.
Yine 1960'da McCrone Associates, tungsten iğneler ve kollodion kullanarak geliştirilmiş parçacık taşıma teknikleri geliştirmeye başladı. Daha sonra endüstri standartları haline gelen bu teknikler, Sınıf 100 (ISO 5) temizoda içine dahil edildi.
1961'de Profesör Sir John Charnley ve Hugh Howorth, Manchester’da bir hastane tavanının çok küçük bir bölümünden direkt olarak ameliyat masasının üzerine aşağı yönlü hava akışı yaratarak tek yönlü hava akışını önemli ölçüde iyileştirmeyi başardı. Ayrıca, 1961'de, temizodalar için yazılmış olan ve Technical Manual TO 00-25-203 olarak bilinen ilk standart, Birleşik Devletler Hava Kuvvetleri tarafından yayınlandı. Bu standart, temizoda tasarımı ve havayla taşınan parçacık standartlarının yanı sıra giriş, giysi ve temizleme prosedürlerini de dikkate aldı. 1962'de, "Ultra Temizoda" olarak bilinen laminer akış odası için 3158457 numaralı Patent yayınlandı. 1965 yılına gelindiğinde 0.46 m/s hava hızının spesifikasyonu ve saatte 20 hava değişimi gereksinimi kabul edilen standart haline geldi. 1970'li yılların başında, "laminer akış" prensibi laboratuvardan üretim ve imalat süreçlerinde de geniş uygulamaya dönüştürüldü.
2000 yılından bu yana, kirlenme riskini azaltırken, üretim ve araştırma süreçlerini hızlandırmaya yardımcı olan yeni temizoda teknolojisinde önemli ilerlemeler kaydedilmiştir. Son yıllardaki teknolojik gelişmelerin çoğu aseptik üretim, yarı iletken ve diğer elektronik bileşenlerin imalatına yönelik olmuştur.
Proseslerdeki zorlukların ölçeği göz önüne alındığında, temizoda teknolojisi önümüzdeki yıllarda üretim için vazgeçilmez olmaya devam edecektir. Bununla birlikte temizodaların dizayn, kurulum ve işletim hataları aseptik proseslerde kabul kriterlerini karşılamayan ürün olarak karşımıza çıkmaktadır. Teknoloji ne kadar gelişirse gelişsin validasyon, sürekli izleme ve doğrulama metotları ile dizaynın, kurulumun ve işletimin amaca uygun olduğunun ispatlanması, özellikle sağlık ve yaşam bilimlerinde bir otorite gerekliliği olarak karşımıza sürekli çıkacaktır.
3. Temizoda Validasyonu ve Validasyon Yaşam Döngüsü
Temizoda ile ilgili birçok standart yazılmıştır. Bu standartlar, temizoda kullanan sektörlerin validasyonlarında yol gösterici olması, personel eğitimi ve kalifikasyonunu denetleyen SOP'lerin yazılması, temizodaların temizliği, bakımı ve temizoda malzemelerinin değerlendirilmesi için çok sayıda bilgi sağlamaktadır.
Validasyona başlamadan önce Validasyon Ana Planı (VMP) mutlaka yazılmalıdır. Bu plan çoğunlukla üç bölümden oluşur: Strateji, Protokoller ve Sonuçları Değerlendirme Raporu.
Yeni bir temizoda validasyonu, belirli bir yaşam döngüsünü izler (Şekil 1). Yaşam döngüsü, her biri modüler ortamdaki değişimi kontrol etmek için belirli görevleri yerine getiren beş fazdan oluşur. Bu fazlar tasarım kontrol aşamasıyla başlar, test etme ve kontrol aşaması ile sona erer. Temizoda validasyonundan sonra ekipman ve kontrol faktörlerinde yapılan değişiklikler, temizodada yeniden validasyon yapılmasına bir gerekçe oluşturur.
![]() |
Şekil 1. Yaşam döngüsü fazları
3.1 Birinci Faz: Tasarım Kalifikasyonu
Temizoda validasyonu, Tasarım Kalifikasyonu (DQ) ile başlar. Bu aşamanın amacı objektif kanıtlarla tasarımın amacına uygun olduğunu ispatlamaktır. Tasarım Kalifikasyonu, DQ protokolünün kabul kriterlerinde tanımlanan gerekliliklere karşı yapılan bir doğrulama çalışması olup, protokol aşağıdaki noktalara değinmelidir:
- Kullanıcı Gereksinimleri Spesifikasyonları (URS)
- Tedarikçi belgeleri ve spesifikasyonları
- Tesis yerleşimi
- Satın alma siparişleri
- Tasarım belgeleri
- Fabrika Kabul Testleri (FAT)
- Yapım çizimleri
- Veri sayfaları
Tasarım Kalifikasyon aşamasının çıktısı bu fazın raporu olup, aşağıdakileri belgeleyen bir Standart Dokümantasyon Listesi (SDL) dosyasıdır:
- Tasarım gereksinimleri
- İhale şartları
- Satın alma ve sipariş belgeleri
- Tedarikçi tarafından sağlanan belgeler listesi
- Yapım çizimleri
- Komponent listeleri
- Kontrol listeleri
- Fabrika Kabul Testleri
Tasarım Kalifikasyonu, DQ aşamasının onayı ve Kurulum Yeterlilik, IQ aşaması için de bir ön gerekliliktir.
3.2 İkinci Aşama: Kurulum Kalifikasyonu (IQ)
Kurulum Kalifikasyon (IQ) aşamasının amacı, kurulumun yapıldığı temizoda ile ilgili tesis, sistem veya ekipmanın kullanıcı gereksinimlerini ve tasarım gereksinimlerini karşıladığını doğrulama yoluyla teyit etmektir.
Doğrulama, IQ protokolü aşağıda adı geçen öğelere odaklanmıştır:
- HVAC cihaz kalibrasyonu
- P&ID şemasının doğrulaması
- HEPA filtre bütünlüğü testi veri incelemesi
- Kritik ekipman kalibrasyon durumu
- Tesis Kabul Testleri (SAT)
- Kurulum Kalifikasyon testleri
- Boru tesisatı ve kaynak belgeleri
- Altyapı doğrulama
- Sistem standart çalışma prosedürleri ve çalışma talimatları
Bu fazın çıktısı, yukarıdaki tüm öğeleri hedefleyen bir IQ raporu ve aşağıdaki öğeleri belgeleyen bir Standart Dokümantasyon Listesi (SDL) dosyası olmalıdır:
- Proje değişiklikleri
- Gerçekleştirilen IQ testleri
- Kalibrasyon
- Tedarikçi tarafından tedarik edilen belgeler
- Ekipman sertifikası
- Kurulum sapmaları
- Tesis Kabul Testleri (SAT)
- Sarf malzemeleri listesi
- Yedek parça listesi
- Çevreyle ilgili inceleme raporu
- Prosedür ve Talimatların Listesi
IQ onayı, İşlevsel (Operasyonel) Kalifikasyon (OQ) aşamasının başlamasının bir ön koşuludur.
3.3 Üçüncü Bölüm: İşlevsel (Operasyonel) Kalifikasyon
İşlevsel (Operasyonel) Kalifikasyon (OQ) aşaması için hedef, objektif kanıtlarla temizodanın tasarım gereksinimlerine ve kullanıcı isteklerine uygun olarak ve belirli koşullar aralığında tutarlı şekilde çalıştığını göstermektir.
OQ protokolü aşağıdakileri ele almalıdır:
- HVAC (Isıtma-Havalandırma-İklimlendirme) sisteminin çalışmasını, belirtilen işlevsel gerekliliklere karşı test etme
- Kritik Alarmlar
- Dahili kilit (interlock) alarmları
- Oda veri (room data sheet) sayfasında tanımlanan kritik işletme parametreleri
- Filtre bütünlüğü testleri
- Temizoda için standart çalışma
- Hava hızı ve hava akışı
- Hava akışı görselleştirilmesi
- Basınç farkı
OQ fazında en kötü senaryolar ele alınmalıdır. Temizoda operasyonu için en kötü senaryoyu oluşturmak amacıyla kritik çalışma parametreleri “temizoda bilgi formu”nda tanımlanır. Her kritik parametre için çalışma aralıkları ve uç nokta aralıklar ayarlanarak, en kötü durum koşulları tasarlanır ve belgelenir. Bu form en az aşağıdakileri içermelidir:
- Maksimum ve minimum sıcaklık
- Maksimum ve minimum nem
- Bakım zamanlamaları
- Personel kirliliği
Genellikle en kötü senaryo, belirtilen en Yüksek ve belirtilen en Düşük parametrelerde gerçekleştirilir. Bu fazın çıktısı, kullanıcı gereksinimi spesifikasyonlarında belirtilen temizoda alarm ve işlevsel gereksinimlerini ele alan bir OQ raporudur ve Performans Kalifikasyon (PQ) aşamasının başlamasının bir ön koşuludur.
3.4 Dördüncü Bölüm: Performans Kalifikasyonu
Temizoda performans kalifikasyonun (PQ) amacı, objektif kanıt ile temizodanın tanımlanan ve istenen çevresel sonucu üretmek için belirlenmiş parametreler arasında sürekli olarak çalıştığını göstermektir. Temizoda performans yeterliliği kullanıldığı sektöre (elektronik, yaşam bilimleri vb.) göre değişmek üzere aşağıdakilerin test edilmesini ve izlenmesini içerir:
- Havadaki partikül seviyeleri
- Yüzeydeki partikül seviyeleri
- Canlı mikrobik partiküller
- Bağıl nem
- Diferansiyel basınç
- Sıcaklık
PQ fazının çıktısı, belirtilen ekipman parametrelerini kullanarak temizoda performansını analiz eden bir PQ raporudur. PQ sertifikasyon için bir ön şarttır.
![]() |
4. Temiz Oda Sertifikasyonu
Valide edilmiş temizodalar, gerekli bir temizlik sınıfı için geçerlidir. Seçilen temizlik düzeyi, kullanıcı gereksinimlerine bağlı olup temizoda sınıfları ISO1464-1'de tanımlanmıştır (Tablo 1).
Sertifikasyon için değerlendirme ve ölçüm yöntemleri ISO14644-3'te belirtilmiştir ve aşağıdaki testleri gerektirir:
- Havada toz partikül sayım testi
- Hava akışı testi
- Hava basıncı farkı testi
- Filtre kaçak testi
- Akış görselleştirme testi
- Hava akışı yönü testi
- Sıcaklık testi
- Nem testi
- Yeniden temizleme (recovery) testi
- Kapalılık (Containment) sızdırma testi
Belli bir sınıfa onay verildikten sonra, parametrelerin kaybolmadığından veya değiştirilmediğinden ve çevrenin kontrol altında olduğundan emin olmak için temizoda parametreleri izlenmeye devam edilir.
5. İzleme ve Kontrol
Sertifikasyondan sonra sabit bir izleme programı gereklidir. Uyumluluk şartları ISO 14644-2'de bulunur (Tablo 2).
Tablo 2. Recommended schedule for testing cleanrooms and clean zones
Test parameter/Performance attribute | Maximum time interval between tests |
Airborne particle concentrations ≤ ISO Class 5 | 6 months |
Airborne particle concentrations > ISO Class 5 | 12 months |
Pressure differentials | Continuously monitored by frequent manual observation or by automated instrumentation |
Installed filter leak test in unidirectional airflow and cleanliness classes ≤ ISO Class 5 | 6 months |
Installed filter leak test in non-unidirectional airflow and cleanliness classes > ISO Class 5 | 12 months |
Airflow velocities in unidirectional airflow | 6 months |
Airflow volume supply in non-unidirectional airflow | 12 months |
Containment leak (optional) | At commissioning, and thereafter every 4 years, or after any significant change to the airflow system or equipment content |
Airflow visualization (optional) | At commissioning, and thereafter every 4 years, or after any significant change to the airflow system or equipment content |
Recovery time in non-unidirectional airflow (optional) | At commissioning, and thereafter every 4 years, or after any significant change to the airflow system or equipment content |
Particle deposition rates (optional) | At commissioning, and thereafter every 4 years, or after any significant change to the airflow system or equipment content |
Segregation tests (optional) | At commissioning, and thereafter every 4 years, or after any significant change to the airflow system or equipment content |
a) Temperature b) Humidity c) Electrostatic and ion generator |
As required, and in agreement with the cleanroom user |
Temizoda parametreleri için istatistiksel analiz, uyumluluğu sağlamak amacıyla sertifikasyondan sonra temizodayı izlemek için bir araç olarak önerilir. Seçilen araç istatistiksel proses kontrolü (SPC)'dür.
Kaynaklar
1. Principles of Cleanroom Validation, 11/06/2011, Comments by David Muchemu
2. Evolution of the Clean Room By John Buie | January 11, 2011
3. ISO 14644-1
4. ISO 14644-2
5. ISO 14644-3
6. T.C. Sağlık Bakanlığı Türki̇ye İlaç ve Tıbbi Cihaz Kurumu Beşeri̇ Tıbbi̇ Ürünler İmalathaneleri̇ İyi̇ İmalat Uygulamaları (GMP) Kılavuzu (2017)
_____________________________________________
Yazar Hakkında
Dilek Sunar 1961 yılı Sarıkamış doğumludur. 1983 yılında İstanbul Üniversitesi Eczacılık Fakültesinden mezun olmuştur. Aynı yıl Eczacıbaşı İlaç Fabrikasında “steril üretim şefi” olarak göreve başlamıştır. 1987 yılında yine aynı firmada GMP uzmanlığına atanmış ve validasyonlardan da sorumlu olarak çalışmalarını sürdürmüştür. 1990-97 yılları arasında Eczacıbaşı Lüleburgaz tesislerinin dizayn ve validasyonlarında görev almıştır. 1998 yılında I.C.C.E.-İstanbul Validasyon ve Eğitim şirketini kurmuştur. 2007 yılında TURKAK tarafından HVAC ve LAF validasyonları için ISO 17020 standardından ilk akredite olan bu firmada genel müdür ve teknik müdür olarak validasyon çalışmalarını devam ettirmektedir.